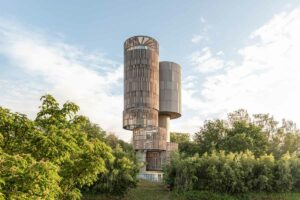
One of the buildings is 220 m long and has 3 electrified tracks. The other is 110 m long. The project can be divided into
4 main parts.
The first one consists of an automated train washing tunnel. This system allows the washing of a complete train (+/- 220 m), like a carwash for cars. The train enters the washing tunnel and the fully automated system performs the external washing without any human participation inside the washing tunnel. A catenary locking system has been installed to comply with safety regulations. When the washing system is in operation, the catenary voltage must be switched off.
In the basement of the building are located all the washing facilities, all the necessary products and a wastewater treatment plant before discharge to the public network.
The second part consists of 2 tracks for the internal washing of trains. They provide access for railway personnel to the interior of the trains for cleaning purposes. These two tracks are equipped with steel structure platforms to facilitate access to the trains. On these platforms, various technical equipments, necessary for the maintenance and the preparation of the trains (city water, compressed air, preheating, Mennekes boxes…), are installed.
The Rapid Repair Center, as its name suggests, is used to perform rapid repair operations. The most important ones will be carried out in the large workshop (building to be built in a later phase). The 3 tracks are equipped with overhead travelling cranes with a lifting capacity of 3.2 To and lateral access platforms to the trains.
While the two tracks are electrified, the third, shorter track is not. It is used for the maintenance of diesel machines. An extraction system is part of the installation to reject the smoke from the machines to the outside. The two electrified tracks are equipped with a retractable catenary to allow the use of the overhead crane. An interlocking system (catenary / overhead crane / gondolas) is installed on the 2 electrified tracks to guarantee the safety of the workers.
Working pits are present under each of the tracks and are supplied with water, compressed air and electricity.
Preheating outlets are installed at the ends of the building. The heating of the hall is done by means of air heaters.
The “office” part also includes changing rooms for the staff of this building. The technical premises include the installations necessary for the operation of the RRC only (medium voltage transformer station, TGBT room, ventilation unit, EV collector, heating, etc.)
The foundations and the “offices/technical rooms” part are made of reinforced concrete. The hall part above the tracks is made of galvanized metal framework. The structure is made up of posts on which trusses are supported and which serve as skylights. In order to bring light into the building, the trusses are covered with polycarbonate. The roof between the trusses is made of galvanized steel sheets type KALZIP. Between the posts of the sails, polycarbonate was also placed for clarity. The walls are made of metal cladding.